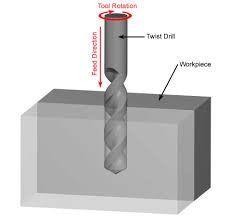
Drilling is one of the most complex machining processes. The chief characteristic that distinguishes it from other machining operations is the combined cutting and extrusion of metal at the chisel edge in the center of the drill. The high-thrust force caused by the feeding motion first extrudes metal under the chisel edge. Then it tends to shear under the action of a negative rake angle tool.
Nomenclature of a Twist Drill — The cutting action along the lips of the drill is not unlike that in other machining processes. Because of variable rake angle and inclination, however, there are differences in the cutting action at various radii on the cutting edges. This is complicated by the constraint of the whole chip on the chip flow at any single point along the lip. Still, the metal-removing action is true cutting, and the problems of variable geometry and constraint are present. Because it is such a small portion of the total drilling operation, though, it is not a distinguishing characteristic of the process.
The machine settings used in drilling reveal some important features of this hole-producing operation. Depth of cut, a fundamental dimension in other cutting processes, corresponds most closely to the drill radius. The un-deformed chip width is equivalent to the length of the drill lip, which depends on the point angle as well as the drill size. For a given set-up, the un-deformed chip width is constant in drilling. The feed dimension specified for drilling is the feed per revolution of the spindle. A more fundamental quantity is the feed per lip. For the common two-flute drill, it is half the feed per revolution. The un-deformed chip thickness differs from the feed per lip depending on the point angle.
The spindle speed is constant for any one operation, while the cutting speed varies all along the cutting edge. Cutting speed is normally computed for the outside diameter. At the center of the chisel edge the cutting speed is zero; at any point on the lip it is proportional to the radius of that point. This variation in cutting speed along the cutting edges is an important characteristic of drilling.
Once the drill engages the workpiece, the contact is continuous until the drill breaks through the bottom of the part or is withdrawn from the hole. In this respect, drilling resembles turning and is unlike milling. Continuous cutting means that steady forces and temperatures may be expected shortly after contact between the drill and the workpiece.
Drill Nomenclature — The most important type of drill is the twist drill. The important nomenclature listed below and illustrated in the figure above.
Drill: A drill is an end-cutting tool for producing holes. It has one or more cutting edges, and flutes to allow fluids to enter and chips to be ejected. The drill is composed of a shank, body and point.
Shank: The shank is the part of the drill that is held and driven. It may be straight or tapered.
Tang: The tang is a flattened portion at the end of the shank that fits into a driving slot of the drill holder on the spindle of the machine.
Body: The body of the drill extends from the shank to the point, and contains the flutes. During sharpening, it is the body of the drill that is partially ground away.
Point: The point is the cutting end of the drill.
Flutes: Flutes are grooves that are cut or formed in the body of the drill to allow fluids to reach the point and chips to reach the workpiece surface. Although straight flutes are used in some cases, they are normally helical.