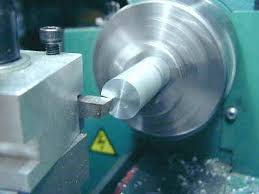
Facing is a fundamental operation that can be done in two basic ways: facing on a lathe and facing on the milling machine. Milling and turning both involve removing material to produce parts with specific features. Facing is the process of removing material from the end and/or shoulder of a workpiece, using a special tool to produce a smooth surface perpendicular to the rotational axis of the workpiece.
When facing on the lathe, the machinist uses a facing tool to cut a flat surface perpendicular to the workpiece’s rotational axis. The facing tool is then fed perpendicularly across the axis. Facing will take the workpiece down to its finished length very accurately: depending on how much material needs to be removed, a machinist can choose to take roughing or finishing cuts.
Lathe facing allows the workpiece to rotate against the cutting tool (which is stationary). There are several factors that can affect the performance of lathe facing operations, including: Type of material the workpiece is made of Size and material of the cutting tool Method of holding the workpiece Speed of rotation Whenever we talk about any facing process, but especially on a lathe, we point out the importance of “qualifying the surface.” In simple terms, qualifying the surface is the process of removing microscopic errors on the workpiece’s surface to make the surface as uniform as possible. When this task can be done, it is always a good practice for machinists. However, if you’re working with a die cast material or a forging, qualifying the surface may not be an option. On the other hand, when facing operations are performed on milling machines, a “live” cutting tool moves and rotates around the workpiece. It’s not uncommon for the milling cutter to have multiple blades or teeth to remove excess material. Face milling can be achieved with a variety of mills. These include: End mill Face mill Shell mill Fly cutter To achieve an optimal surface finish, it’s best to let the machine feed the table: CNC machines and newer manual machines have this capability, but older ones generally do not. There is also a specific type of face milling known as spotfacing, which faces localized areas such as the bearing surfaces on which bolt heads or washers will sit.