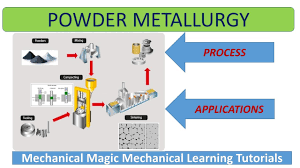
Powder metallurgy is the process of blending fine powdered materials, pressing them into a desired shape or form (compacting), and then heating the compressed material in a controlled atmosphere to bond the material (sintering).
The powder metallurgy process consists of four basic steps:
Powder manufacture
Powder blending
Compacting
Sintering
Compacting is generally performed at room temperature, and the elevated-temperature process of sintering is usually conducted at atmospheric pressure. Optional secondary processing often follows to obtain special properties or enhanced precision.
The high-precision forming capability of PM generates components with near-net shape, intricate features and good dimensional precision pieces. The unique flexibility of the PM process enables products to be made from materials that are tailored to users' specific needs. By using specially selected materials, this capability enables refinements to be engineered into the mechanical properties of the part.
The PM process has the highest raw material utilization (over 95%) and the lowest energy requirement per kilogram of finished part, compared with other manufacturing processes. It is suitable for high-volume production with very little wastage of material. Secondary machining is virtually eliminated.
Powder metallurgy is a continually and rapidly evolving technology embracing most metallic and alloy materials, and a wide variety of shapes. It is a highly developed method of manufacturing reliable ferrous and non-ferrous parts. The expansion of the automotive industry in the U.S., has been a big influence. Over 90% of powder metallurgy products are used in the transportation market.
Powder metallurgy parts are used in a variety of end products such as:
Hardware
Automobile parts
Washing machines
Power tools
Copiers and postage meters
Hunting knives
Hydraulic assemblies
X-ray shielding
Oil and gas drilling well-head components
The PM process provides a host of advantages over competing metalworking technologies, including:
Cost effectiveness
Shape and material flexibility
Application versatility
Part-to-part uniformity
Powder metallurgy also recognized as "green" technology.